7 Benefits of Predictive Maintenance Software- How to Choose the Right One?
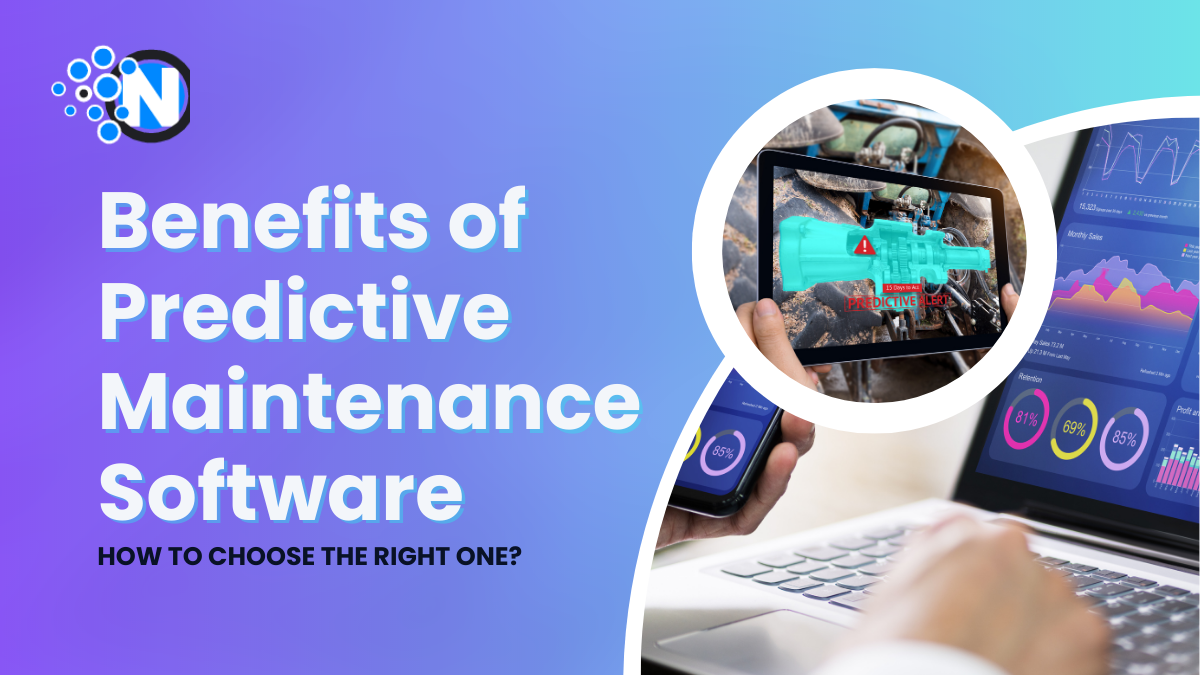
Companies from different industries constantly struggle to streamline operations and reduce downtime in this modern business landscape. One important aspect of achieving this goal is the effective management of maintenance activities. Traditional maintenance methods, like reactive or preventive maintenance, are limited in terms of cost-effectiveness and efficiency. That’s where predictive maintenance software comes into play. With the help of advanced analytics and ML algorithms, predictive maintenance software offers several benefits to businesses, helping them improve equipment reliability, increase productivity, and reduce maintenance costs.
This blog post has listed some key benefits of using predictive maintenance software and tips for choosing the right software for your business.
What is Predictive Maintenance?
Predictive maintenance is a maintenance strategy that leverages data analysis and predictive analytics technologies to forecast when equipment failures can occur. By monitoring the condition and performance of equipment in real-time and analyzing historical data, predictive maintenance helps businesses identify potential issues before they cause expensive breakdowns.
Benefits of Predictive Maintenance Software
Predictive maintenance software plays a crucial role in implementing this strategy effectively, offering several benefits to companies across various industries.
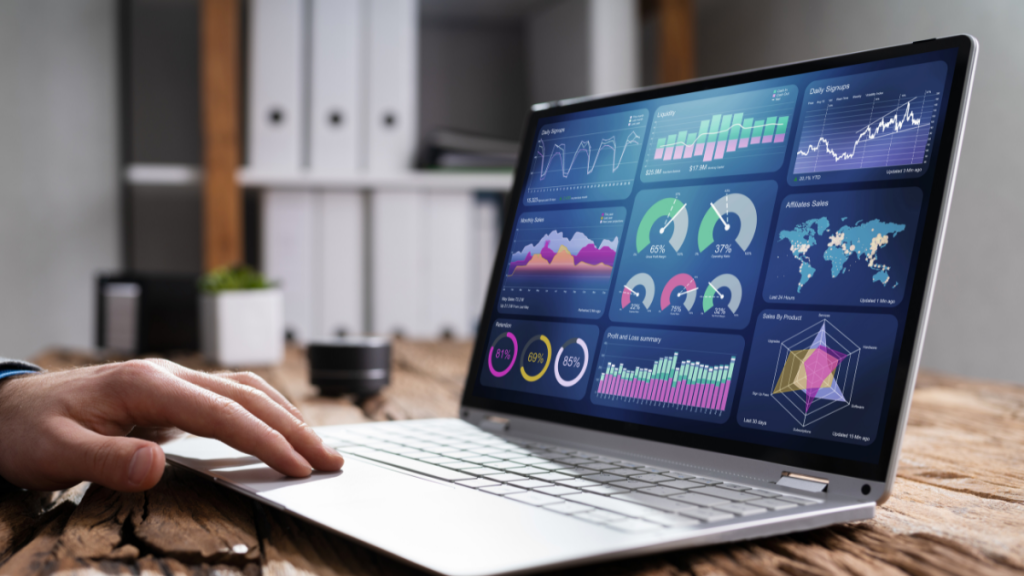
1. Increased Equipment Uptime
One of the primary benefits of predictive maintenance software is the increased uptime of equipment. By continuously monitoring equipment conditions and detecting early signs of potential failures, businesses can take proactive measures to prevent unexpected breakdowns. This allows for timely maintenance interventions, reducing unplanned downtime and ensuring that equipment remains operational for longer periods. Improved equipment uptime enhances productivity, minimizes production losses, and improves customer satisfaction.
2. Reduced Costs
Predictive maintenance software helps businesses achieve significant cost savings by optimizing maintenance activities. Traditional maintenance approaches often involve either reactive maintenance, where repairs are performed after a breakdown occurs, or preventive maintenance, which involves performing maintenance tasks at regular intervals regardless of the actual equipment condition. Both approaches can lead to unnecessary costs. On the other hand, predictive maintenance software enables businesses to schedule maintenance tasks based on actual equipment health, minimizing unnecessary interventions and maximizing the cost-effectiveness of maintenance operations.
3. Enhanced Maintenance Planning
With predictive maintenance software, maintenance planning becomes more efficient and effective. The software collects and analyzes data from various sources, such as sensors, equipment logs, and maintenance records, to provide insights into equipment health and performance. This enables maintenance teams to prioritize tasks based on criticality and allocate resources appropriately. By clearly understanding the equipment’s condition and performance, businesses can optimize maintenance schedules, reduce downtime, and streamline their overall maintenance operations.
4. Improved Safety and Risk Management
Predictive maintenance software improves safety and risk management by enabling early detection of equipment anomalies or degradation. By continuously monitoring equipment health, the software can identify potential safety risks and alert maintenance teams to take immediate action. By addressing issues early, businesses can avoid accidents, injuries, and costly damages that may arise from catastrophic equipment failures. Timely maintenance interventions reduce the chances of accidents caused by faulty equipment, ensuring a safe working environment for employees and minimizing potential risks to the surrounding environment.
5. Extended Equipment Lifespan
Regular maintenance based on the actual condition of the equipment helps extend its lifespan. Predictive maintenance software allows businesses to detect and address issues early, preventing further deterioration and minimizing the chances of major failures. By identifying and resolving problems early, companies can ensure that equipment operates optimally for longer, reducing the need for premature replacements. This saves on equipment costs and maximizes the return on investment for existing assets.
6. Increased Operational Efficiency
Predictive maintenance software plays a significant role in improving operational efficiency. By adopting a proactive approach to maintenance, businesses can avoid costly disruptions caused by unexpected breakdowns. Scheduled maintenance tasks can be planned during planned downtime or off-peak periods, minimizing the impact on production schedules. Furthermore, the software provides valuable insights into equipment performance and utilization, enabling businesses to optimize asset allocation, streamline workflows, and improve overall operational efficiency.
7. Data-Driven Decision Making
Predictive maintenance software empowers businesses with data-driven decision making. The software generates valuable insights into equipment performance trends, failure patterns, and maintenance requirements by analyzing vast amounts of equipment data. These insights enable informed decision making regarding maintenance strategies, spare parts inventory management, equipment upgrades, and replacements. By leveraging the power of data, businesses can optimize maintenance practices, reduce costs, and drive continuous improvement across their operations.
How to Choose the Right Predictive Maintenance Software?
1. Data Integration Capabilities
One of the first considerations when selecting predictive maintenance software is its data integration capabilities. Seamlessly integration with various data sources, such as sensors, equipment logs, and maintenance records is an important thing to consider when choosing a software solution for your business. It should be able to collect and analyze data from these sources in real-time to provide accurate insights into equipment health and performance. Robust data integration capabilities ensure the software can effectively monitor equipment conditions and deliver reliable predictive maintenance recommendations.
2. Advanced Analytics and Machine Learning
Effective predictive maintenance software relies on advanced analytics and machine learning algorithms to process large volumes of data and identify patterns or anomalies. The software should have robust analytical capabilities to derive actionable insights from the collected data. Look for a predictive maintenance software solution that uses machine learning algorithms to continuously learn from past data and improve the accuracy of predictions over time. Advanced analytics and machine learning technologies enable the software to provide accurate and reliable predictions, allowing maintenance teams to make informed decisions.
3. Real-Time Monitoring and Alerts
Timeliness is crucial in predictive maintenance. The software should offer real-time monitoring of equipment conditions and provide instant alerts when anomalies or potential failures are detected. This ensures that maintenance teams can respond promptly to critical situations and prevent unexpected breakdowns. Look for software solutions that offer customizable alerting mechanisms, allowing you to set thresholds and notification preferences according to your specific requirements. Real-time monitoring and alerts enable proactive maintenance interventions and minimize downtime.
4. User-Friendly Interface
Good predictive maintenance software always has a user-friendly interface that is intuitive and easy to navigate. The software should also present data and insights in a clear and concise manner, to enable users to understand the information immediately. A user-friendly interface streamlines the adoption and usage of the software, ensuring that maintenance teams can quickly leverage its capabilities without extensive training or technical expertise. Find software solutions that offer customizable dashboards and reports, allowing you to adjust the interface to your needs.
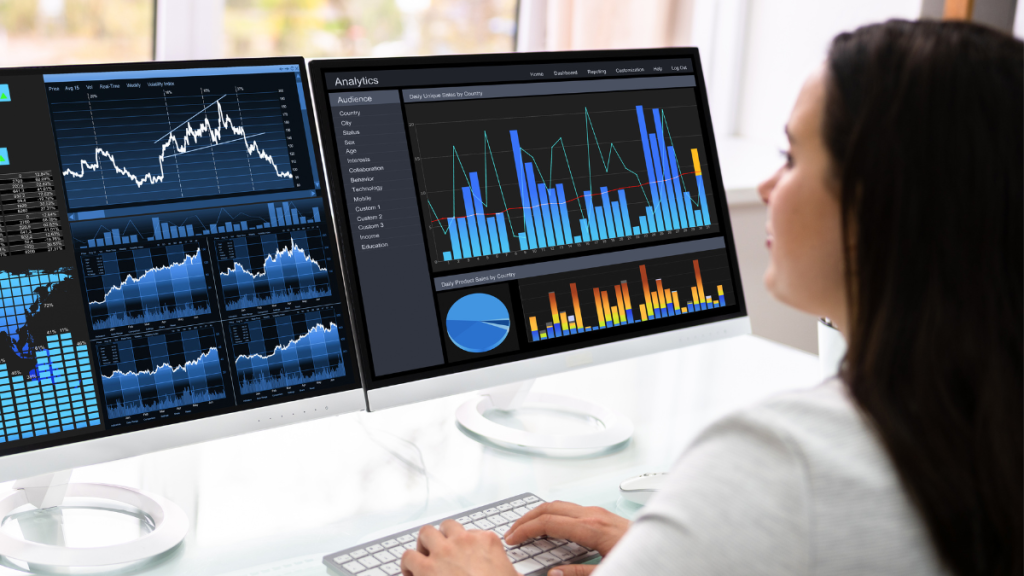
5. Integration with Existing Systems
Evaluate whether the predictive maintenance software can seamlessly integrate with your existing systems and software solutions. It should be able to integrate with your enterprise resource planning (ERP) system, asset management software, and other relevant tools to streamline data flow and enable cross-functional collaboration. Integrating existing systems reduces data silos, enhances data accuracy, and facilitates a holistic view of organizational maintenance operations.
6. Vendor Support and Reputation
Consider the vendor’s support and reputation in the industry. Choose a reputable vendor with a track record of delivering reliable, high-quality software solutions. Evaluate their customer support services, including training, technical assistance, and software updates. A vendor with a strong reputation and excellent customer support ensures a smooth implementation and ongoing support for your predictive maintenance software.
Final Thoughts
Predictive maintenance software offers numerous benefits to businesses seeking to enhance their maintenance operations. From increased equipment uptime and cost savings to improved safety, extended equipment lifespan, and data-driven decision-making, the software enables companies to proactively manage their assets, reduce downtime, and optimize maintenance activities. By implementing predictive maintenance software, businesses can stay ahead of equipment failures, improve operational efficiency, and achieve a competitive edge in today’s rapidly evolving business landscape.